At a laboratory in Newark, New Jersey, a gray liquid swirls vigorously inside a reactor the size of a small watermelon. Here, scientists with the mining technology startup Still Bright are using a rare metal, vanadium, to extract a common one, copper, from ores that are too difficult or costly for the mining industry to process today.
If the promising results Still Bright is seeing in beakers and bottles can be replicated at much larger scales, it could unlock vast copper resources for the energy transition.
Still Bright isn’t the only company seeking to revolutionize copper production. A handful of startups with similar goals have announced partnerships with major mining firms and scooped up tens of millions of dollars of investment. These companies claim their technology can help meet humanity’s surging appetite for the metal, while driving down the industry’s environmental footprint.
“We’re facing unprecedented demand for copper, and that’s really tied to the electrification of everything,” Still Bright chief of staff Carter Schmitt told Grist.
Still Bright
The world cannot reach its climate goals without copper, which plays a central role in the technologies needed to decarbonize. Copper wiring is at the core of the world’s electricity networks, which will have to expand enormously to bring more renewable energy online. Wind turbines, solar panels, electric vehicles, and lithium-ion batteries all rely on the mineral, too. As the market for these technologies grows, the clean energy sector’s demand for the 29th element is expected to nearly triple by 2040.
At the same time, copper miners are exhausting their best-quality reserves. Copper that is economical to mine is found in rocks known as ores, and grades of the ores that miners are exploiting — the concentration of copper contained in them — have declined steadily over the past 20 years. Meanwhile, easy-to-process minerals near the surface are giving way to more challenging ones deeper down. And the current standard procedure for extracting the metal from the majority of ores results in a lot of pollution.
About 80 percent of the copper mined today comes from unweathered rocks known as primary copper sulfide ores. After being crushed and ground to a fine powder, the copper inside primary sulfide ores is concentrated using chemicals before being sent to a smelter, where it is refined at high temperatures.
The process of concentrating and smelting copper produces a toxic mineral slurry called tailings, and a cocktail of air pollutants including lead and arsenic. In the United States, a single Native American tribe — the San Carlos Apache people — has borne the brunt of that pollution. Two of America’s three copper smelters are located within a few miles of the tribe’s reservation boundaries in southeastern Arizona. Both are among the worst lead emitters in the nation, spewing toxic metals into the air for the better part of a century. (One of these smelters was mothballed four years ago following a labor strike, but is reportedly planning to resume operations to meet surging copper demand.)
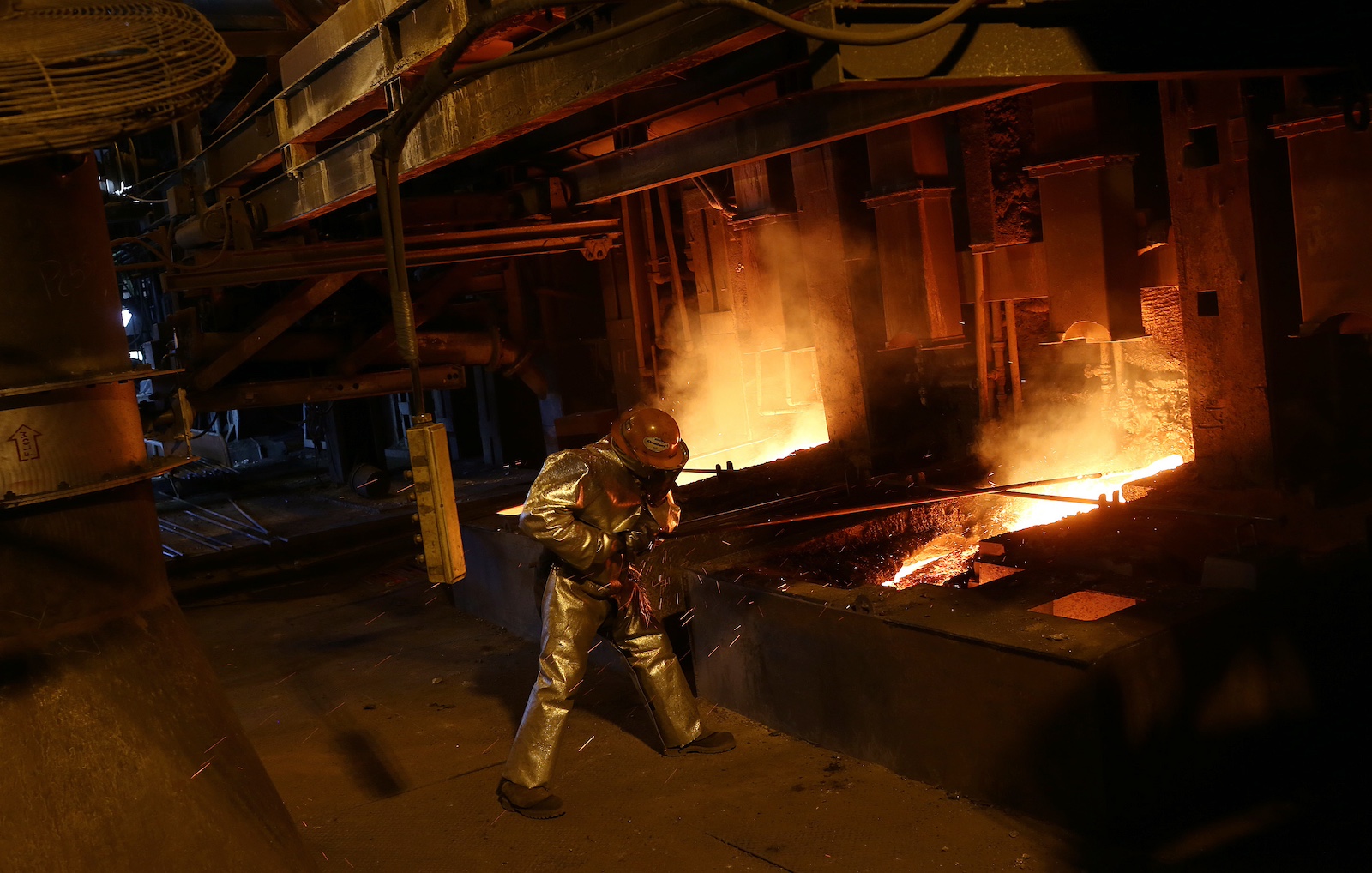
Andrew Lichtenstein / Corbis via Getty Images
“This stuff doesn’t go away,” says Jim Pew, the director of clean air practice at the environmental law firm Earthjustice, told Grist. “It falls back to the Earth and permanently contaminates the communities nearby.” (The San Carlos Apache Tribe didn’t reply to Grist’s request for comment.)
In addition to air pollutants, copper smelters are energy intensive and typically require fossil fuels, driving up costs as well as carbon emissions. If the ore is too low-grade (meaning the concentration of copper is too low) companies simply can’t get enough out to cover the cost of extracting it.
But globally, low-grade primary sulfide ores contain enormous amounts of copper. A March report by Goldman Sachs estimated that the world’s top five copper miners are sitting on “billions of tons” of such ores — an amount that makes the expected 5 to 6 million ton copper supply shortfall over the next decade look puny.
“It’s not that the world is out of copper,” Cristobal Undurraga, CEO of the Santiago, Chile-based startup Ceibo, told Grist. “It is, though, in a form … harder to extract using traditional processes.”
Founded in 2021, Ceibo is one of several mining technology startups that’s proposing a new, old approach to getting copper out of low-grade sulfide ores: a process known as heap leaching. Heap leaching is already used to process the weathered rocks located toward the top of most deposits, which account for about 20 percent of copper mined today. Miners process these rocks on site by crushing the rock, piling it up into a heap, and spraying it with acid, which percolates through the rock and liberates the valuable metal. The process produces significantly less pollution and carbon emissions than traditional copper smelting — but until recently, no one has figured out how to make it work efficiently for primary sulfide ores.

Thomas Ingersoll / courtesy of Jetti Resources
Ceibo claims it is able to recover large quantities of copper with a chemical extraction approach that involves altering critical conditions in the crushed ore, such as the pH and oxygen concentration, making it easier for the acid to get to work. Ceibo says its process is flexible and can accommodate the wide variety of geologic and environmental conditions a company might encounter in different parts of the world — or even different parts of the same subterranean pit. “What we are developing is a whole geological platform” that can be adjusted based on those changing conditions, chief technology officer Catalina Urrejola told Grist.
Ceibo hasn’t revealed many details of its process, which it has mostly tested at the laboratory scale. But the firm has already secured $36 million in venture capital financing to scale up, including funding from major industry players like BHP Ventures, the investment arm of one of the world’s largest copper producers. In November, Ceibo began its first pilot tests with Glencore’s Lomas Bayas Mining Company, based in Chile’s Atacama Desert.
Another mining startup, Jetti Resources, is already processing primary sulfide ores commercially using heap leaching. The Colorado-based company has developed a proprietary catalyst that alters the surface of the crushed minerals, helping acid penetrate to extract the copper. In 2019, Jetti began deploying its technology commercially at Capstone Copper’s Pinto Valley mine in Arizona. At leaching sites where the firm’s catalyst is being used, Jetti says it has doubled production.
“We believe that our catalyst is the only commercially available technology for economically producing copper from chalcopyrite,” a primary sulfide mineral that represents about 70 percent of untapped copper reserves, chief technology officer Nelson Mora told Grist in an email.

Thomas Ingersoll / courtesy of Jetti Resources
Holly Bridgwater, director of Australian mining innovation company Unearthed Solutions, thinks the technology startups like Ceibo and Jetti are offering holds promise — despite a lack of public test results.
“Otherwise, all these mining companies wouldn’t be working with them,” she said. “They would have stopped the trials way earlier if it wasn’t demonstrating value.”
Still, heap leaching has economic and technological limitations. It can take weeks to months for the chemicals to work their way through a rock pile to extract the copper, which is typically less than 1 percent of the material present. And no company is claiming it can extract everything. Jetti told Grist its process can recover 40 to 70 percent of the copper from chalcopyrite, compared to 15 to 30 percent for “conventional leaching processes.” Undurrago said Ceibo’s technology can recover 70 to 80 percent of the copper from primary sulfide ores in a “reasonable timeframe.”
By contrast, Still Bright claims it can extract up to 99 percent of the copper from primary sulfide ores in a matter of minutes.
Still Bright’s technology, called “electrochemical reductive leaching,” starts with a copper concentrate similar to what smelters work with. Instead of smelting the metal, Still Bright combines it with a solution of liquid vanadium. The vanadium reacts with the copper, liberating it from the sulfide minerals, before being recycled in an electrolyzer that takes inspiration from vanadium flow batteries. Like heap leaching, this process can take place on-site at a mine in one of Still Bright’s “stirred tank reactors,” rather than at a separate smelting facility.
The key advantage of Still Bright’s tech, Schmitt says, is that vanadium and copper react incredibly strongly with each other. “You can extract copper really easily and really quickly at ambient temperature and pressure,” Schmitt said.
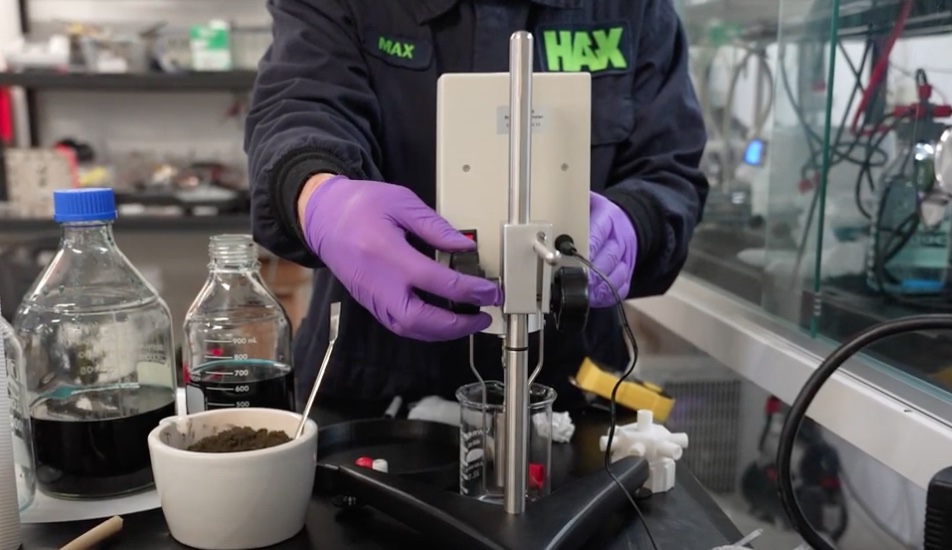
Still Bright
Initially, Still Bright plans to market its tech as a way to extract copper from particularly challenging ores that can’t be smelted today, as well as from mine waste. Eventually, it hopes to offer a more sustainable alternative to smelting for high-grade copper sulfide ores, too. While Still Bright’s process produces some tailings, it avoids the toxic air pollutants tied to smelting, and potentially the carbon emissions. Because Still Bright’s equipment is fully electric, it can be powered by renewable energy, Schmitt says.
Still Bright has validated its process at a lab scale and is working on setting up its first in-house pilot project, which it anticipates completing by 2026.
Pew, the Earthjustice attorney, declined to comment on the viability of these new technologies as a replacement for copper smelting. But finding alternative ways to refine copper, he says, is “very important” for ensuring vulnerable communities aren’t left footing the bill.
“We’re going to be using copper for a long time to come,” Pew said. “We should be thinking how do we get that copper without these ancient technologies that pollute so much.”
While Schmitt and others are hopeful they can bring cleaner refining methods to market, copper mining has additional impacts that improved processing techniques can’t address. No matter what extraction technology is used, copper mines can destroy habitats, create dust and water pollution, deplete freshwater supplies, and interfere with Indigenous peoples’ access to cultural practices and sacred sites. The industry is facing significant backlash over these impacts, with activists and regulators stalling and shutting down major projects in recent years. In Panama, the government recently ordered the shutdown of a major copper mine following mass protests over the threat it posed to water supplies and a court order deeming the project unconstitutional. In Arizona, an indigenous group is fighting to block Rio Tinto and BHP from mining a giant copper reserve that lies beneath lands considered sacred.
Thea Riofrancos, a political scientist at Providence College who studies resource extraction and climate change, says it is “noteworthy” that many of the mining giants pouring money into new copper processing methods — a list that includes Rio Tinto and BHP — are also being criticized over the harmful effects of mining. Whether or not these firms are planning more sweeping environmental reforms, Riofrancos says their investment in clean tech startups draws attention to the fact that the mining industry, along with many climate investors, is beginning to brand resource extraction as a climate solution.
“This is an emerging focus in the venture capital world — supporting early-stage startups in the critical mineral space,” Schmitt said. “At all stages: the mining, crushing, grinding, and onward to refining, … it’s all needed.”
Editor’s note: Earthjustice is an advertiser with Grist. Advertisers have no role in Grist’s editorial decisions.